A team of MIT engineers has successfully designed a new material with five percent the density of steel and ten times the strength, making it one of the strongest, lightweight materials known. The material was developed by compressing and fusing flakes of graphene, a two-dimensional form of carbon. After many years of hard and devoted work, the scientists have finally translated these 2D structures of into 3D graphene.
The findings are being reported a few days ago in the journal Science Advances, in a paper by Markus Buehler, the head of Massachusetts Institute of Technology (MIT) Department of Civil and Environmental Engineering (CEE) and the McAfee Professor of Engineering; Zhao Qin, a CEE research scientist; Gang Seob Jung, a graduate student; and Min Jeong Kang MEng ’16, a recent graduate.
Graphene – “wonder material”
Graphene is an allotrope of carbon in the form of a two-dimensional, atomic-scale, hexagonal lattice in which one atom forms each vertex.
This “wonder material” according to the American Physical Society, is about 200 times stronger than the strongest steel. It has extraordinary conductivity, flexibility, and transparency.
Andre Geim and Konstantin Novoselov, who discovered this material in 2004, won the 2010 Nobel Prize in Physics.
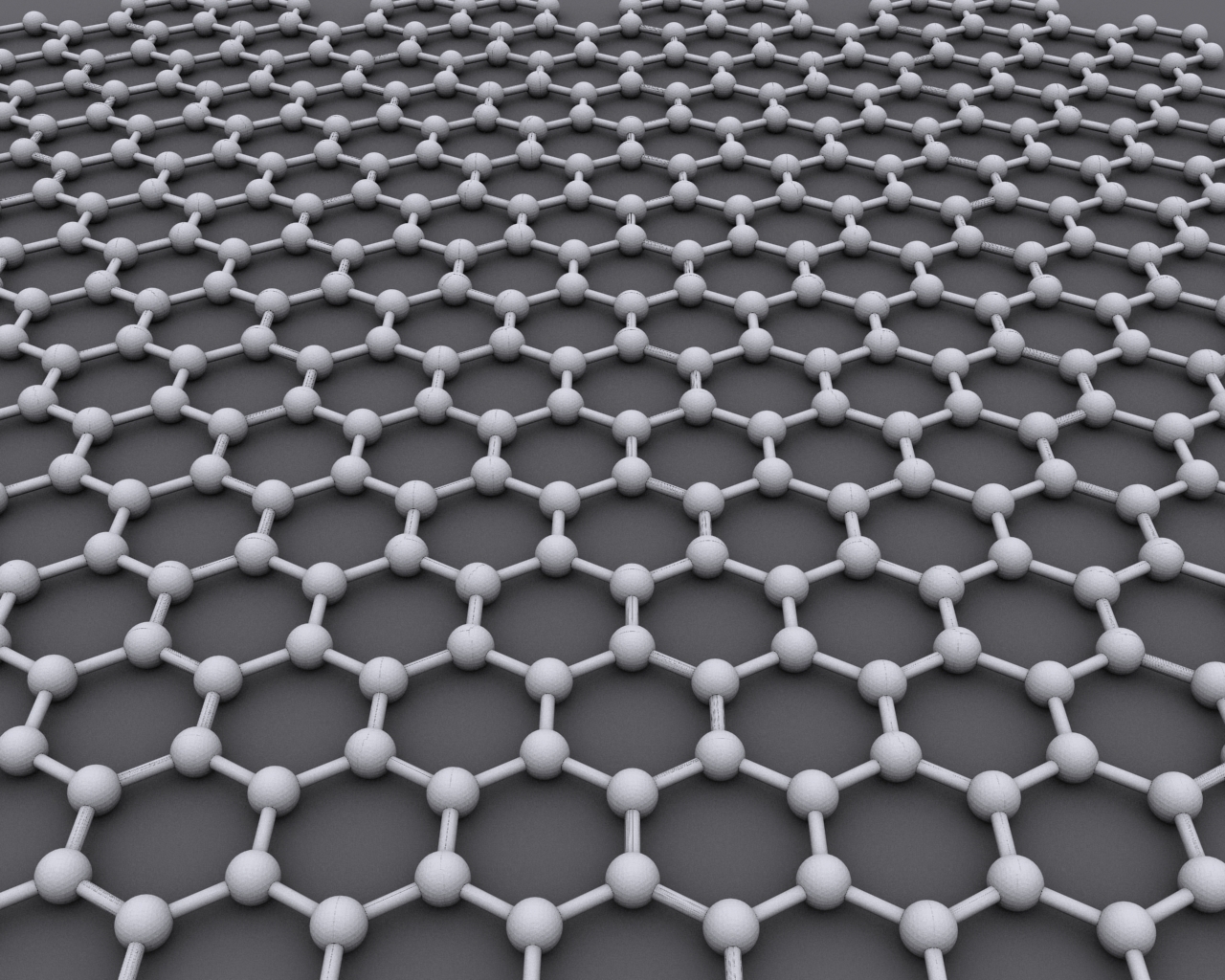
Graphene is a thin layer of pure carbon; it is a single, tightly packed layer of carbon atoms that are bonded together in a hexagonal honeycomb lattice. Until the 3d graphene configuration, this 2D configuration was the strongest and lightest material.
In its two-dimensional form, graphene is thought to be the strongest of all known materials. For many years, scientists have believed they could create a 3D graphene to improve abilities of two-dimensional configuration.
And now, for the first time the MIT team was able to compress small flakes of graphene using a combination of heat and pressure.
3D Graphene
Creating a computer simulation of the material, the researchers were able to test different geometrical formations to find the strongest shape.
3-D graphene looks something like a Nerf ball. It is round but it is full of holes, called gyroids. This unusual configuration makes this complex material probably impossible to be made by using conventional manufacturing.
That’s why 3D graphene has been made in the lab using a high-resolution, multimaterial 3D printer. Actually, graphene produced from natural graphite is the most useful starting material for the production of graphene-infused polymers used to make 3D printing filaments.
To explain how 3D material behaves, Buehler compares it to sheets of paper. Though paper has little strength along its length and width, it can gain the strength when formed into specific shapes.
For example, when you roll the paper into a tube, suddenly the strength along the length of the tube is much greater and can support substantial weight.
Similarly, 3D graphene composed of curved surfaces under deformation can make a very strong configuration after pressure and heat treatment.
Geometry – dominant factor in future development of materials
The new findings show that the crucial aspect of the new 3D forms is their extraordinary geometrical configuration. The aspects of this material don’t depend on the material itself.
That suggests the possibility of creating 3D forms of various materials by creating similar geometric features.
“You can replace the material itself with anything,” Buehler says. “Actually, the geometry is the dominant factor. It’s something that has the potential to transfer to many things.”
For example, concrete for a structure such a bridge might be made with this porous geometry, providing comparable strength with a fraction of the weight. This approach would have the additional benefit of providing good insulation because of large amount of enclosed airspace within it, Myscience explains.